Multi-layer co-extrusion high barrier film is generally produced by multi-layer co-extrusion blowing or casting process. The film has excellent barrier, mechanical, stretch forming and heat sealing performance. It does not require additional lamination during processing, and it is not involved in the problems such as printing ink, adhesive and additive residues. Therefore, it is a relatively green and cost-effective food packaging technology.
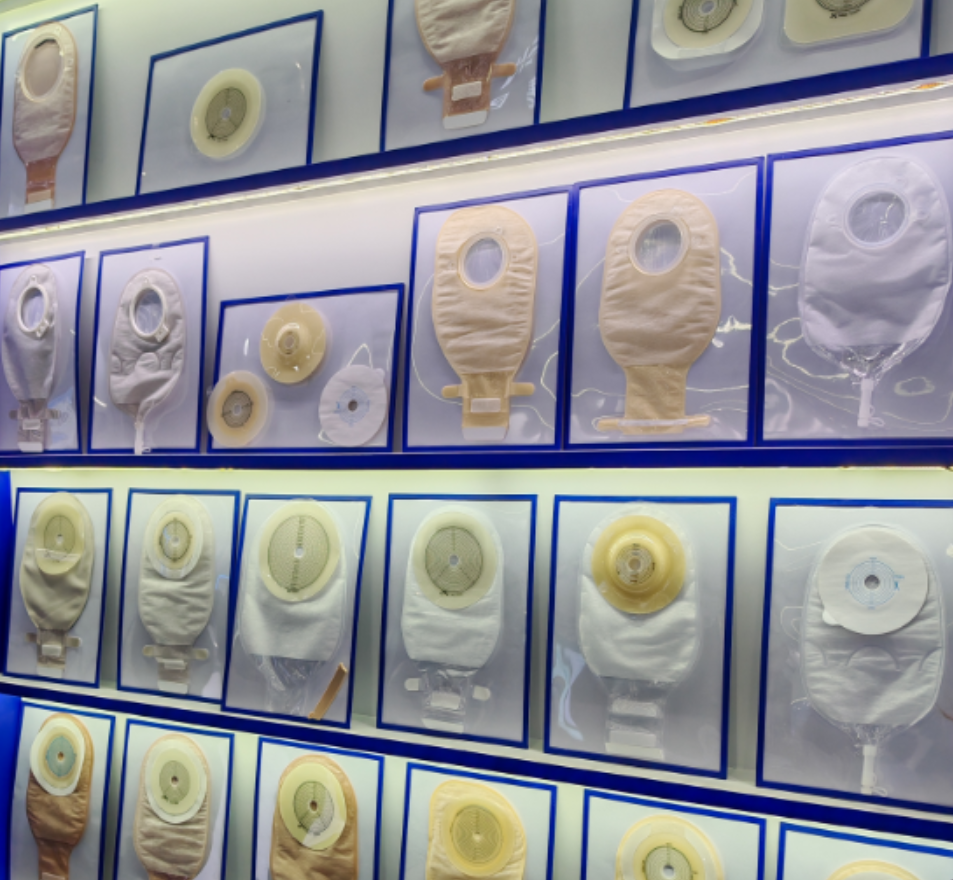
Multi-layer co-extrusion high barrier film refers to the use of 3-11 or more extruders to distribute and melt resin raw materials with different functions, such as polyethylene, polypropylene, nylon, ethylene-vinyl alcohol copolymer, etc., through its flowing channel to meet at the co-extrusion die head. And then they are cooled and compounded together after blow molding or casting to produce a multi-layer co-extrusion film. The advantages can produce films with comprehensive performance that meets different packaging needs.
- The advantages of multi-layer materials
The multi-layer co-extrusion barrier film structure can combine materials with different properties according to needs, so that it can have multiple properties at the same time. For example, for heat sealing and packaging machinery, the film needs to have good mechanical processing properties, and MDPE or HDPE material is used in the multi-layer structure to improve the strength and stiffness of the film and ensure good mechanical processing properties. The inner layer is made of metallocene polyethylene material with good heat sealing performance, so that the film has good heat sealing performance and mechanical properties to better meet packaging needs. In order to meet different barrier needs, we can make PA co-extrusion barrier film, EVOH co-extrusion barrier film, PVDC co-extrusion barrier film, etc.
- Cost control
Multi-layer co-extrusion barrier film technology is a multi-layer co-extrusion one-time molding process. It does not require traditional post-processing processes such as compounding and coating. It effectively reduces raw material costs and production processes. It not only saves production costs, but also improves film thickness to achieve the feasibility of thinning.
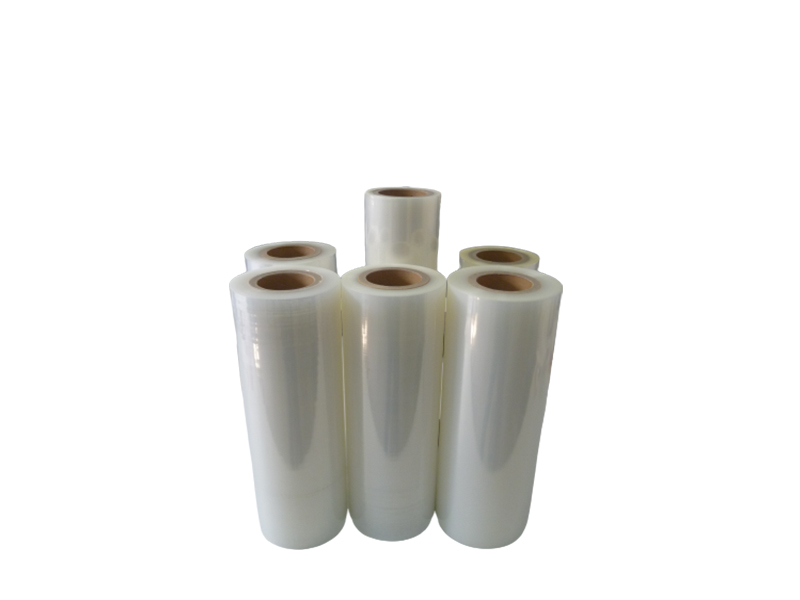
- Flexible structure
Through structural design, the film is desinged in different combinations. More co-extruded layers there are, greater the flexibility in structural design is. Currently, the multi-layer co-extrusion film structure on the market has reached a maximum of 11 layers. It is possible to realize high barrier film, medium barrier film and low barrier film because of flexible design of the multi-layer co-extrusion structure. The film colors are also achieved according to different color masterbatch.
- Wide range of applications
- Ostomy bag
- Screw Cap for Wine Bottle
- Processed-Meat Packaging
- Beverage Packaging
- Bottle Cap Liner
- Pharmaceutical packaging
- Protective Clothing
Structural design of multi-layer co-extrusion films
The structure of multi-layer co-extrusion films can be divided into two categories, namely symmetrical structure (A/B/A) and asymmetrical structure (A/B/C).
At present, the majority of barrier films are 5, 7, 8, 9, 10 and 11 layers. Taking a 5-layer co-extrusion film as an example to introduce the relevant structure. The symmetrical structural layer of the multi-layer co-extrusion barrier film consists of 3 types of functional layers: barrier layer, adhesive layer and support layer.
Barrier layer: The barrier layer has the functions barrier protection against oxygen, water vapor, odors or numerous chemical agents. Barrier materials in the market include PA, EVOH and PVDC, etc.
Support layer: Generally, symmetrical structural materials have two support layers. The inner layer is used for heat sealing, The outer layer is directly used as packaging layer or printing layer. The support layer requires good mechanical strength, heat sealing performance, water vapor resistance, transparency and printability. The regular materials for this layer are LDPE, LDPE/LLDPE, PP or EVA.
Adhesive layer: The role of the adhesive layer is to bond the barrier layer and the support layer to ensure the peeling force between layers.

- Symmetrical structure barrier film
PE/Tie/PA/Tie/PE
PE/Tie/PVDC/Tie/PE
PE/PE/Tie/PVDC/Tie/PE/PE
EVA/Tie/PVDC/Tie/EVA
EVA/EVA/Tie/PVDC/Tie/EVA/EVA
PE/Tie/EVOH/Tie/PE
PE/Tie/PA/EVOH/PA/Tie/PE
PE/PE/Tie/PA/EVOH/PA/Tie/PE/PE
PE/PE/PE/Tie/PA/EVOH/PA/Tie/PE/PE/PE
- Asymmetric structure barrier film
PA/Tie/PE/Tie/PA/Tie/PE
PA/Tie/PP/Tie/PA/Tie/PP
PA/Tie/PE/Tie/PA/EVOH/PA/Tie/PE
PA/Tie/PP/Tie/PA/EVOH/PA/Tie/PP
PA/PA/PA/EVOH/PA/Tie/PP/PP/PP/PP